CEMS Installation & Startup
Each shelter is shipped on a flatbed truck ready to be placed on a slab, pad, or other mountings. After a CEMS Shelter is permanently installed at the site, the shelter undergoes a functionality test during the startup of the plant to ensure that it is ready for use. The shelter installation is verified by connecting the components to the plant utilities and communications and then testing for the proper operation of the CEMS hardware and software.
For the startup, all PLC signals, alarms, and communications are verified with the plant control center after connection. The heated sample line, probe support bundle, and cylinder gases are installed. All equipment and components installed on the shelter are checked once more for functionality.
Our Field Service Technician performs a leak check, calibrates the analyzers, and verifies the startup and shutdown conditions programmed in the CEMS DAHS. The technician demonstrates basic functions like how to perform a calibration check or adjust flows and pressures. Basic troubleshooting of the CEMS system is also discussed.
Startup services can be stand-alone or combined with Certification services.
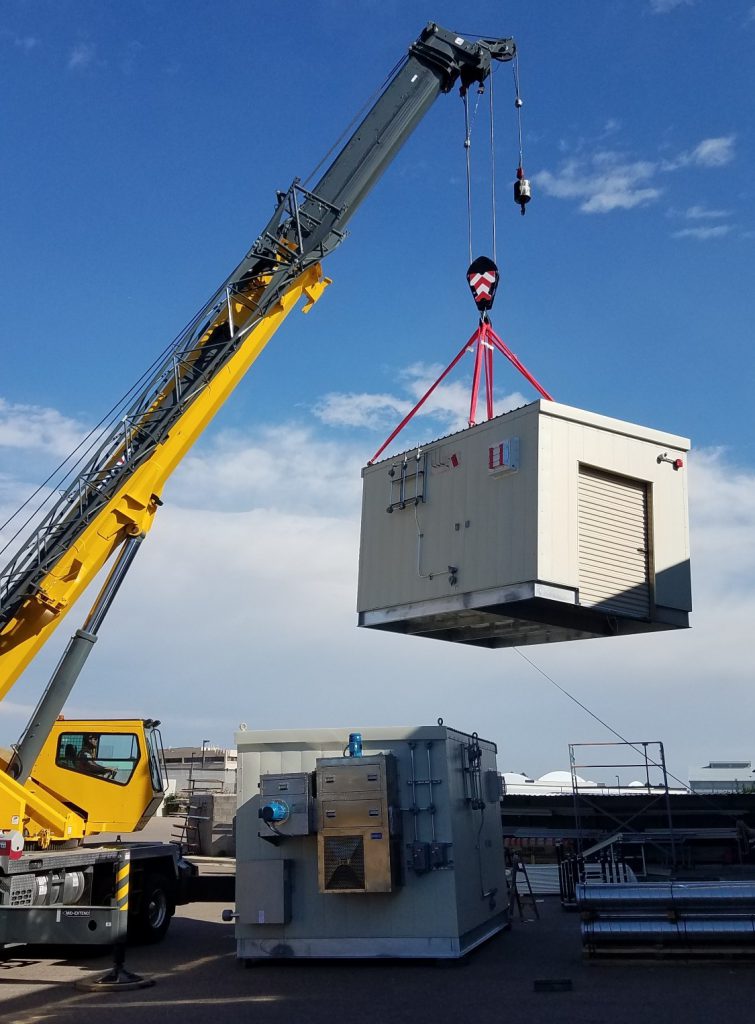